Guidelines For Cleaning Pharmaceutical Processing Equipment
Tweet
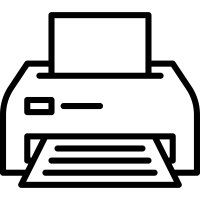
Cleaning pharmaceutical processing equipment is challenging. Cleaning methods, soils present, type of manufacturing equipment, surfaces cleaned, choice of cleaning detergent and temperature should all be considered when setting up a cleaning procedure. Cleaning validation methods are required. The entire cleaning process must be standardized and documented according to the FDA’s cGMP regulations.
Why Clean Pharmaceutical Processing Equipment?
- Maintain product quality.
- Remove all trace ingredients to prevent the transfer of ingredients from one product to the next. This is especially important when multiple products are produced on the same equipment.
- Prevent equipment malfunctions that may lead to product contamination.
- Provide a clean surface for disinfection. Surfaces cannot be properly sanitized or disinfected if they are not thoroughly cleaned first.
- Comply with local and international standards and regulations to ensure consumer safety and avoid legal issues.
- Increase plant performance and productivity by diminishing waste, maintaining equipment and preserving product quality.
- Enhance worker safety by providing a clean working environment and smoothly functioning equipment.
Establishing A Cleaning Procedure
Federal Regulations
Pharmaceutical manufacturers are required to set up a fully documented written cleaning procedure for each piece of processing equipment in compliance with FDA 21 CFR Part 211.67. Documentation should include:
- Responsibility for equipment cleaning and maintenance
- Cleaning and sanitization schedules
- A detailed description of the cleaning procedure
- Removal of previous batch identification
- Protection of clean equipment
- Inspection of equipment prior to use
Manufacturers must outline each of these steps in detail to be sure that all processes are followed clearly and succinctly.
Cleaning Procedures
Federal regulations require a very specific description of each step of the cleaning procedure. The following details should be documented.
- Frequency of cleaning – including time requirements between processing products and cleaning
- Cleaning tools used – any sponges, brushes, scrapers, sprayers, wipes or equipment used to aid the cleaning process
- Establishment and sequence of each cleaning step
- Identification of each specific piece of equipment to be cleaned, including instructions for cleaning between batches of the same or different products
- Cleaning method – clean-in-place (CIP) or clean-out-of-place (COP)
- Detailed instructions for any required disassembly and re-assembly of equipment if COP methods are used. Instructions should specify the parts to be removed and any assembly aids used during this process.
- Identification of all cleaning detergents and detailed instructions for their use. Usage instructions should include amounts, concentration, temperature, dwell time and application method.
- Type of water – deionized, distilled or tap
- Number of rinse steps required
- Drying and storage guidelines
- Instructions for visual inspection after cleaning
- Cleaning validation methods
How to Clean
Several factors must be taken into consideration to set up an effective cleaning process and remain in compliance with federal regulations.
Soils
Soils found on pharmaceutical processing equipment may be traces of the various ingredients used in production or soils from the actual manufacturing process such as oil, grease, dust or minerals. Understanding the soils that are present will guide your choice of cleaning detergent.
Gels, polyethylene glycol, oils, titanium dioxide, dyes, silicons, flavorings, petrolatum, paraffin, proteins, steroids, sugars, alcohol, stearates, and cornstarch are some of the typical foulants that are often found on pharmaceutical processing equipment.
Each type of soil is unique and requires the proper detergent to thoroughly clean the surface. Choose a cleaner that will best attack the soils you are trying to remove. Alkaline cleaners are the best choice for cleaning soils such as gels, dyes and petrolatum, while citric acid based cleaners are better suited for removing titanium dioxide. Protein or starch-based soils may require the use of an enzyme cleaner. Use the table below to help match the most effective type of cleaner to each kind of soil.
Type of Equipment
Mixing tanks, tablet presses, capsule fillers, centrifuges, granulators, filling lines, mixers, conveyors, filters, fluid lines, batch process tanks, tubes and flasks all need to be thoroughly cleaned. The design of the equipment must be taken into consideration. By nature of its construction, some types of equipment will be more difficult to clean than others. Hidden parts and blind holes present unique challenges.
Another important factor to consider is the how the equipment is used. Are you cleaning a dedicated production system or equipment that is used to produce a range of products? Processing equipment used to produce multiple products has a greater chance of cross contamination of ingredients.
It’s also important to select a cleaner that is compatible with the surface of the equipment you are cleaning. The cleaner manufacturer should be able to guide you and provide compatibility studies for their products.
Cleaning Method and Location
Clean-in-place (CIP) or Clean-out-of-place (COP)?
CIP is generally used for large systems and components that cannot easily be taken apart. CIP often results in less downtime since it eliminates the need to take apart or move the equipment. Automated systems, spray systems and immersion are all examples of CIP operations.
COP is most often used for smaller pieces of equipment or smaller parts of larger equipment that can be removed and re-assembled after cleaning. COP can involve either manual washing or use of machine washers. Specific instructions for disassembling and re-assembling equipment must be followed.
What cleaning method will you use?
Manual, ultrasonic, spray, machine and automated systems are all used for cleaning pharmaceutical equipment. The type of cleaning method used will impact your choice of detergent. Automatic parts cleaners and high-pressure washers require low foaming detergents.
Temperature
In most cases, increasing the temperature is one of the best ways to speed up or improve the cleaning action. The temperature parameters that should be used for any individual cleaning application will depend upon the equipment and the soils that are present, as well as your choice of detergent and wash method. Check with the manufacturer for the maximum suggested operating temperature for your detergent.
Dwell Time
The length of the cleaning cycle contributes to the effectiveness of your cleaning application. In most cases, a longer dwell time will improve the results. However, all factors – soils, temperature, substrate, detergent and cleaning method must be taken into consideration.
Rinse Step
Thorough rinsing should follow cleaning. Rinsing removes any excess detergent left on the item. For critical cleaning applications, it is best to use deionized or distilled water, as rinsing with ordinary water may introduce new contaminants.
Cleaning Validation
Cleaning validation is a part of the regulatory compliance process for cleaning pharmaceutical processing equipment. Validation ensures that all equipment is washed according to previously determined standards and that all traces of soil and detergent are removed. Validation methods are unique to each detergent and should be available from most cleaner manufacturers.
Download IPC’s “7 Step Guide to the Proper Usage of Critical Cleaners” for more information on establishing a cleaning regimen.
Need help choosing the right specialty cleaner for your pharmaceutical cleaning application? Contact one of International Products Corporation’s (IPC) technical specialists or request a free cleaner sample for testing. All of IPC’s specialty cleaners are registered with NSF as A1 cleaners and can be validated in FDA processes.
Tweet
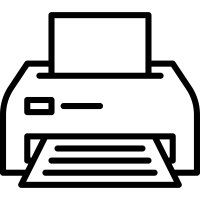