Special P-80 Formulas…Perfect For Pumps In The Food Industry
Tweet
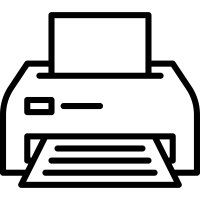
Pumps and seals perform vital functions in food and beverage processing plants. Using the right assembly lubricant for pump maintenance makes all the difference.
Manufacturing facilities strive to keep operations running smoothly and effectively at all times. This is true for all types of plants, whether they manufacture industrial products or foods and beverages. While many factors contribute to achieving this goal, one simple way to help reach this objective is to perform regular equipment maintenance. Most plants use a variety of different types of pumps. Maintaining and replacing pump seals on a regular basis helps to ensure that systems continue to function efficiently.
Replacing standard pump components, such as seals, O-rings, and other rubber parts, can often lead to frustration because the slip resistant nature of rubber makes it difficult to install, cut, remove or manipulate. Parts may roll or tear. Repair and installation can take considerable physical effort and time. In addition, improper part alignment or installation can lead to part failure and safety issues.
Pumps play an extremely important role in food and beverage manufacturing. They are used for fermentation, separation, evaporation, homogenization, filtration, processing and dosing. Mechanical seals are frequently used to help ensure that no contaminants enter the processing system.
Mechanical seals help to minimize leaks, avoid flow irregularities and maintain product integrity. They can help prevent the transfer of ingredients from one product to the next, and prevent formation of deposits inside the pump that can develop into mold or bacteria, causing contamination.
Food processing plants have added concerns that must be considered. Food and beverage manufacturing is a highly regulated industry. Therefore, all parts and processes must comply with federal regulations and industry standards. Mechanical seals need to be made of food grade materials, and all lubricants used for seal maintenance must also be approved for incidental food contact applications.
Properly functioning pumps help plant managers in food and beverage manufacturing plants address the following concerns and challenges:
• Safe and hygienic processing
• Cleanliness
• Quality standards
• Traceability
• Product integrity
• Safety
• Regulatory compliance
• Risks of contaminants entering the system
• Avoidance of trace ingredients and impurities during manufacturing
Just like in industrial settings, pumps used in the food industry should be well maintained to avoid costly repairs and minimize downtime. Maintenance procedures must meet strict FDA and USDA requirements.
Using the proper assembly lubricant can turn a difficult chore into an easy task. Many jobs can benefit from the reduced friction and increased safety provided by an assembly lubricant. They are the perfect solution for pump and seal repairs and have been used for years by plant managers to maintain equipment and replace parts such as mechanical seals, O-rings, hoses, grommets, and plugs.
Temporary rubber assembly lubricants can:
Reduce Installation Force: A thin film of lubricant allows rubber surfaces to slide across each other. By reducing the surface tension between two surfaces, lubricants help rubber parts slide easily into place. Once dry the lubrication is gone, resulting in a tight fitting assembly.
Achieve Closer Fits: Engineers can design lower tolerance parts. The force needed to install the parts when a lubricant is used is greatly reduced. Since the lubrication is only temporary, once dry, the parts stay in place resulting in a tight fit.
Improve Product Performance: Improper part alignment can lead to part failure and safety issues. Using a rubber assembly lubricant, which enables the parts to slide easily into place, can solve these problems by reducing or eliminating damage to parts.
Increase Production Rates: Applying an assembly lubricant to the rubber part makes the rubber slippery, so parts can easily slide into place. After the lubricant dries, the lubricity goes away and mated parts maintain a tight fit. The assembly process becomes more productive.
Help to Avoid Worker Injuries: Lubricants reduce the insertion force needed for rubber assembly. Workers can more easily push parts into place, reducing the amount of musculoskeletal, slippage, and repetitive stress related injuries that can be caused by using too much force to insert a rubber part.
There are many types of lubricants available, so how does a plant manager choose the right one for the job? It’s important to consider the performance and safety of each to make the right choice.
Types of lubricants:
Solvents offer poor lubrication (as compared to other choices). More importantly, these substances may be flammable and pose various safety risks. They may also dry out the rubber parts.
Soaps and Detergents offer nominal lubricity but can reactivate later on when wet, causing parts to move when they need to remain stationary.
Petroleum Distillates are often not compatible with rubber parts causing them to swell. The lubrication is not temporary.
Specially Formulated Ester Based Products offer temporary lubrication providing excellent reduction in friction. These lubricants are safe for the environment, the parts and the workers.
Plant managers need to choose a lubricant that will work well, yet meet all safety requirements and federal regulations. They must also consider variables unique to their specific needs such as surface compatibility, dry time, conductivity and chemical composition of the lubricant.
Specially formulated, temporary rubber assembly lubricants are a preferred choice. They have a consistent composition, favorable compatibility with most surfaces and are not harmful to the environment. In fact, many of these lubricants are biodegradable. Food and beverage processing facilities must also be sure to use specially formulated temporary assembly lubricants that meet federal regulations and are approved for incidental food contact applications.
Many food and beverage processing plants rely on P-80® Temporary Rubber Assembly Lubricants to help with pump maintenance. P-80 lubricants enable rubber parts to slide easily into place with minimal force. Once dry, P-80 stops lubricating and parts remain in place, resulting in a tight fit. Since P-80 does not contain silicon or any other persistent ingredients, once dry the slipping action goes away. P-80® Emulsion IFC and P-80® THIX IFC meet FDA regulation 21 CFR 178.3570 and are NSF-Registered as H1 lubricants. Both are biodegradable and non-toxic, ideal for use in incidental food contact applications when a thin film of lubricant is desired.
The next time you’re having trouble replacing a pump seal, inserting a grommet, or pushing a hose into place, try using a temporary rubber assembly lubricant. See how much easier the job becomes.
Tweet
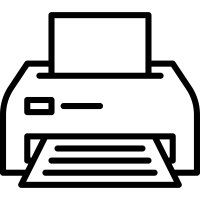